Alfa Laval Spirals. The future starts here.
Are you looking for more uptime and twice the thermal efficiency of a comparable shell-and-tube? A spiral heat exchanger might be the answer. It has a quick payback time, with low installation and operating costs. Since 1962, Alfa Laval has helped more than 5,000 customers with their challenges, delivering more than 80,000 spirals. Could you be next?
Solving the toughest challenges
Do you need a heat exchanger that’s a true workhorse? With an ingenious design that prevents fouling and keeps it working longer between cleanings, you can count on a spiral heat exchanger from Alfa Laval to get the job done – year after year.
75 years of partnership and innovation
Spiral heat exchangers from Alfa Laval are designed to deliver – for licensors, EPC contractors and end-users. They handle the heaviest heat transfer demands, even with dirty or viscous media. Best of all, we’re dedicated to building long-term partnerships that are as reliable as our heat exchangers themselves – and last just as long.
Improving sustainability with Alfa Laval’s spiral heat exchangers
Alfa Laval spiral heat exchangers are designed to handle the toughest heat transfer challenges, such as frequent fouling from dirty media or limitations from pressure drop and floor space.
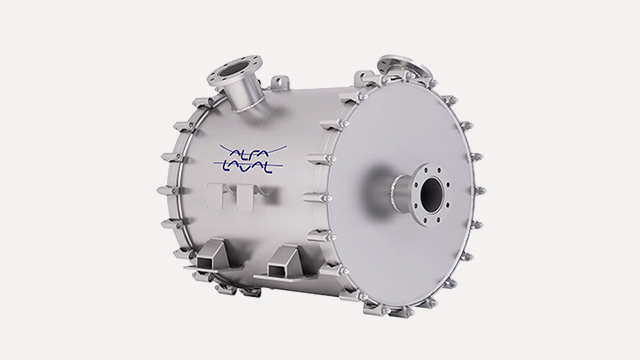
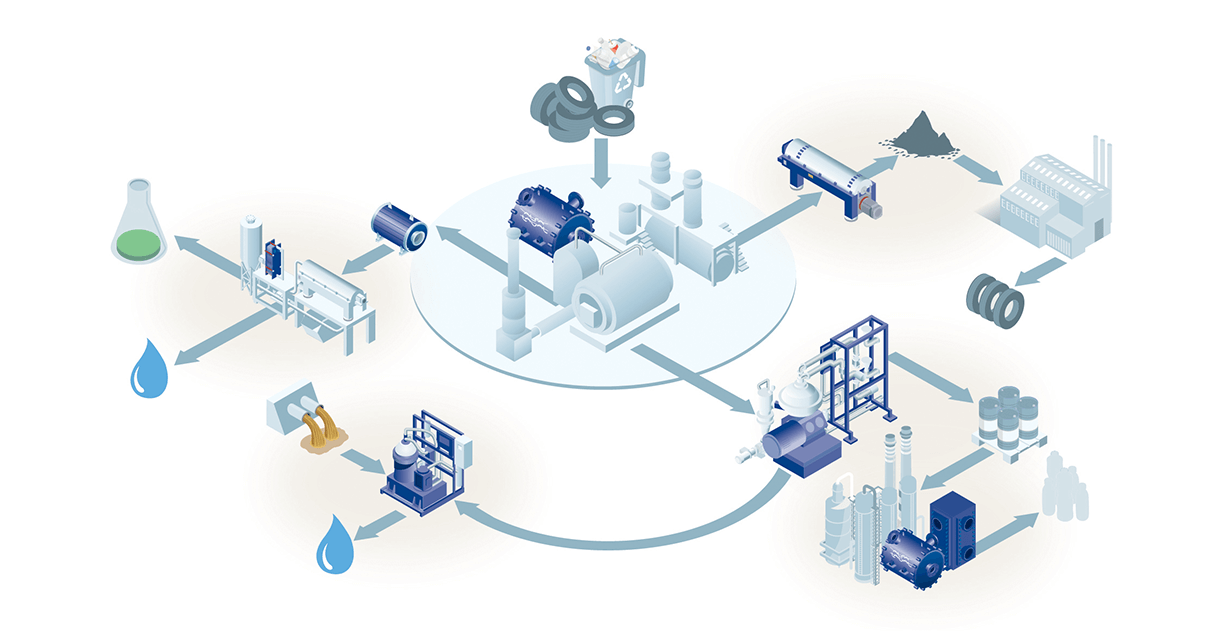
Spirals in Pyrolysis
To reach our collective climate goals on time, we need to reuse and recycle as much as we can. Chemical recycling is just one example of how. Pyrolysis is a form of chemical recycling that supports circularity in the harder to abate sectors, as plastic waste and used tyres can be gathered, pyrolyzed to create a synthetic oil, and separated for reuse as a circular feedstock. As you can imagine, this is a messy process that comes with a heavy dose of fouling media and a high likelihood for corrosion.
Alfa Laval was the first company to introduce spiral technology to the world of heat transfer; a design so reliable that it is still number one today. Now, we want to bring this robust technology into the world of plastic recycling. Thanks to its single channel design, this heat exchanger can cope with all kinds of heavy-duty inlet media to make even the stickiest substance easy to process. It uses the high-density deposits that naturally occur to increase velocity and even self-clean, making it the perfect partner for processing heavy oils. With the support of this technology, we hope to open the door to new possibilities in the recycling industry for a cleaner tomorrow.
Sustain efficiency with our ten top tips for spiral heat exchangers
Do you have a spiral heat exchanger? We want to share our best practices for maintaining consistently high performance, maximum operational reliability, and exceptional energy efficiency. We’ve created a new series of videos that show you how to perform maintenance safely and how to keep your heat exchangers in the best possible condition.
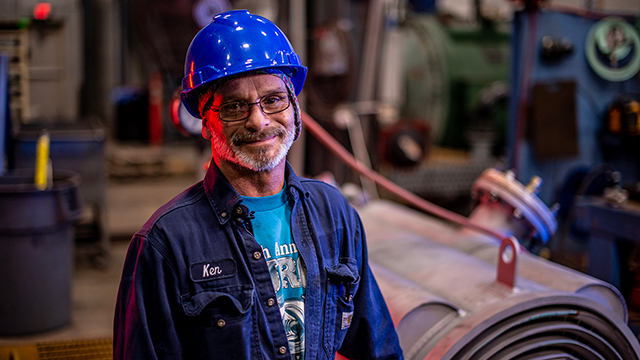